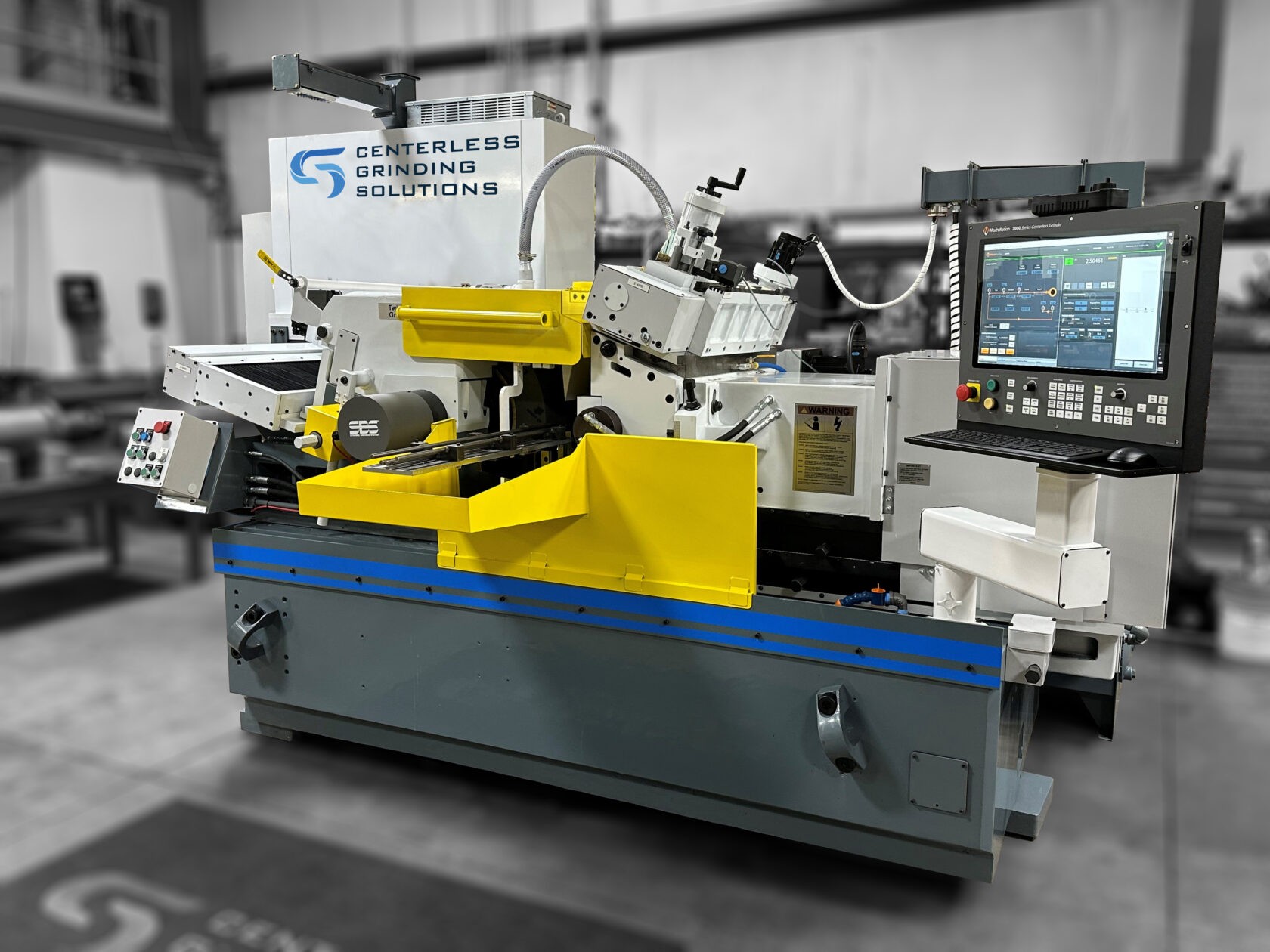
3 Types of Centerless Grinding: Exploring the Path to Flawless Finishes
Have you ever marveled at the precision of cylindrical parts in various industries, from automotive to aerospace? The secret behind these flawlessly finished surfaces is often centerless grinding, a pivotal manufacturing process that ensures smooth and precise outcomes. This method, distinguished by its ability to shape materials without holding the workpiece through traditional methods, offers a blend of speed and precision unmatched by conventional grinding techniques.
Centerless grinding is categorized into three primary types, each suited to different needs and applications. Through-feed, in-feed (plunge), and end-feed grinding offer unique advantages and cater to various machining requirements. Exploring these methods provides insight into how manufacturers achieve such flawless finishes and why centerless grinding is critical in producing high-precision parts.
Overview of Centerless Grinding
Centerless grinding, a cornerstone in precision machining, eliminates the need for fixtures or clamps to hold workpieces. Instead, the process relies on two rotating wheels to grind and guide the part. The absence of a spindle or fixture allows for a seamless operation, significantly enhancing efficiency and precision. This method is particularly advantageous for high-volume production, where consistency and speed are paramount.
The technique is celebrated for producing parts with smooth, round surfaces to a high degree of accuracy. Industries such as automotive and aerospace, where precision is non-negotiable, frequently employ centerless grinding to meet their exacting standards. The process is not just limited to metal parts but also applies to a wide range of materials, making it a versatile choice for various manufacturing needs.
1. Through-Feed Centerless Grinding
Through-feed grinding is the most straightforward and widely used centerless grinding method, ideal for parts with a consistent diameter throughout their length. In this process, the workpiece enters the grinding zone from one side. It exits from the opposite side without lateral movement, making it exceptionally efficient for long, straight parts such as rods and bars.
The key to through-feed centerless grinding is the setup, where the workpiece is supported by a work rest blade and is sandwiched between a rotating grinding wheel and a slower-speed regulating wheel. The regulating wheel, angled slightly to the grinding wheel, controls the workpiece’s rotational speed and axial feed. This setup allows for rapid material removal, producing a smooth surface finish with remarkable efficiency.
Through-feed grinding’s primary advantage lies in its ability to quickly process cylindrical parts with minimal intervention, making it a preferred choice for high-volume production runs. Its simplicity and effectiveness in producing straight, cylindrical parts make it an indispensable technique in the manufacturing sector.
2. In-Feed (Plunge) Centerless Grinding
In-feed, also known as plunge centerless grinding, is tailored for parts with complex shapes or varied diameters, making it the go-to method for components that cannot be processed through the through-feed method. This process involves manually placing the workpiece into the grinding machine, which remains stationary as the grinding wheel moves to shape the specific area or feature.
This method grins parts with intricate profiles, such as notches, steps, or other detailed features. The precision and control offered by in-feed grinding make it possible to achieve tight tolerances and complex geometries, often required in specialized applications. Unlike through-feed grinding, in-feed grinding does not require the part to have a uniform diameter along its length, allowing for greater versatility in the types of parts that can be processed.
In-feed grinding is particularly useful for short production runs where each part may have different grinding requirements. The setup for each part can be customized, providing the flexibility needed to handle complex grinding tasks efficiently.
3. End-Feed Centerless Grinding
End-feed centerless grinding is designed explicitly for tapered workpieces and other parts with a complex shape with varying diameters. In this method, the workpiece is fed into the machine on one end and rests against an end stop; then, the grinding operation is performed. The workpiece moves linearly through the machine, allowing the grinding wheel to shape the part to its final tapered or contoured form.
This process is beneficial for components that require a precise tapered surface, as it allows for the gradual shaping of the part’s profile as it passes through the grinding wheels. The control over the feed rate and the precise positioning of the workpiece makes end-feed grinding an excellent choice for parts that cannot be efficiently or accurately ground using through-feed or in-feed grinding methods.
End-feed grinding’s unique capability to produce complex shapes makes it valuable for manufacturing specialized components in industries where precision is critical, such as aerospace and automotive engineering. The method’s ability to handle parts with intricate geometries ensures that even the most challenging design specifications can be precisely met.
Comparing the Three Types
Having explored the nuances of through-feed, in-feed (plunge), and end-feed centerless grinding, it’s evident that each method brings its advantages to the manufacturing table. Through-feed grinding is the epitome of efficiency, perfect for high-volume production of uniform cylindrical parts. In-feed grinding, on the other hand, offers unmatched precision for complex shapes, making it ideal for components requiring intricate detailing. End-feed grinding excels in shaping parts with tapered or precisely contoured ends, providing the precision needed for specialized applications.
The choice among these three methods hinges on the specific requirements of the part being produced. Factors such as the part’s geometry, the desired finish, production volume, and the shapes’ complexity play a crucial role in determining the most suitable grinding technique.
Conclusion
The art of centerless grinding is a cornerstone in precision manufacturing, providing a path to flawless finishes and parts that meet stringent tolerance requirements. Understanding the distinctions between through-feed, in-feed, and end-feed grinding allows manufacturers to choose the optimal process for their specific needs, ensuring efficiency, precision, and quality in every piece. As manufacturing challenges evolve, so will the techniques and technologies in centerless grinding, continuing to play a vital role in producing precision parts across various industries.
Are you in pursuit of precision and efficiency for your manufacturing needs? Explore the benefits of centerless grinding with our expert team. Contact us today to discover how our centerless grinding services can enhance your production process and deliver the high-quality parts your projects demand.